How to make a juicer for apples from a variety of materials with their own hands
One of the easiest ways to process a crop is juicing. Apple JuicerDIY-made can be a great solution, because most of these devices are either expensive or have low productivity and short-lived.
Content
From the machine with horizontal loading
There are several ways to make centrifugal juicer from washing machine. For one of them you will need a drum, its mount and casing from horizontal machine.
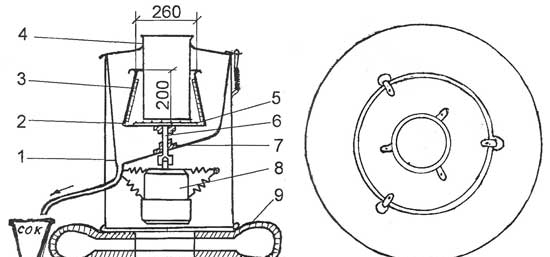
The design of a homemade juicer from a washing machine: 1 - washing machine tank; 2 - centrifuge; 3 - mesh liner; 4 - bunker for fruit; 5 - grater; 6 - sleeve axle; 7 - guide pipe; 8 - the engine; 9 - car tire.
First, they are cleaned from traces of powder and scale, and then polished to a shine with fine emery paper. All the holes in the drum casing, except for the bottom one, are covered with a thin rubber gasket and stainless steel plates with nuts and bolts.
From a sheet of stainless steel, 2-3 mm thick, a circle with a radius of 110-115 mm is cut for the grater. For the lining we make another circle of the same diameter and of the same material, but already 0.5-0.6 mm thick. Lining provides rigidity. It is fastened with three brass struts exactly in the middle of the bottom of the drum. The grout is set on the lining with five M5 screws.
Through two circles, many holes are drilled, with a radius of 2.5 mm, a centimeter marking is drawn across the diameter, dividing it into 14-20 sections. On it the cutting teeth are filled by a punch.
The loading tube for apples, corresponding to the diameter of a large hole, is attached to the drum from four sides with aluminum corners on the bolts. It is possible to use a pipe with corrugated hose or a polyethylene pipe with walls 5–6 mm thick. MB bolts are inserted from the inside of the casing at the beginning of the process and are clamped from the outside with nuts.The distance between the pipe and the grater determines degree of grinding apples. From above corners are fixed by sheepskin.
Stainless steel mesh with a 1 × 1 mm cell is used to make blanks with dimensions with a drum section (with a margin of one centimeter for bending) according to the number of stiffeners. Bend the grid so that the edges become smooth and safe. Rivet gun and awl tightly attach the mesh to the drum.
For the pusher, a plywood circle with a diameter of 0.8-0.9 cm is mounted on the end of a thick cutting from a shovel. A limiter is installed to prevent the pusher from touching the float.
The pulley is modified to fit the required dimensions and the V-belt. The base frame is welded from the corner. Ideal engine 1.1 kW at 3000 rpm.
A polyethylene or rubber circle is cut with a diameter like that of a casing and a hole corresponding to the diameter of the pipe for loading apples. This cover protects against splashes and closes the moving drum. A hose for the outgoing juice is pulled to the lower opening of the drum, under which the pan is placed.
All elements are firmly clamped, the motor and wires are insulated, the voltage in the network is taken into account. Details of the tank are thoroughly washed.
During the test run, an empty drum of a properly assembled homemade apple juicer should not beat and produce foreign noise.
Apples are laid in it for 2-3 pieces. Push them close to the grater. Centrifugal force distributes the cake on the grid. If the device starts to vibrate, then without adding apples, wait until the juice stops flowing. If the product is laid in a planned and continuous manner, a bucket of apples will be processed before vibration (within 7–10 minutes).
After turning off the engine with a plastic spatula, remove the cake from the grid. Then we wash and dry all the details. The device is stored disassembled.
From the activator type machine
Centrifugal Juicer can also be made from activator type washing machine. The activator and the shaft are removed from the bottom of the tank, set the shaft of the desired diameter. Three knives are mounted on a shaft thread with nuts at an angle of 60 degrees. The drain hole closes. The stainless steel mesh with a cell of approximately 1.5 mm is laid on the wall of a centrifuge with an overlap of 40-50 mm. At the bottom put the complete rubber cover, plugged cork. All washed with baking soda. Timer relays disconnect or wedge his toggle switch.
Apples of several pieces are lowered into the tank on moving knives. Fruits are ground for 20-30 minutes. Over time the centrifuge is moved no more than 3 liters obtained mashed potatoes so that it does not spill out. After 2-3 minutes removed the grid with waste.
The assembled machine prepares 10-12 liters of juice with pulp per hour, works with juicy fruits. To remove the sediment, defend the juice, and then pass through the gauze.
Apple Press
If there is no electricity, a homemade juicer is best done in the form of a press. Apples for her are cut in half, removed the core and rotted areas. The long straight trough of pine or spruce boards is filled with prepared apples, which are then pushed with a rectangular spatula with a sharp blade and a width corresponding to the trough.
In a rectangular tank, pan, barrel, or wooden compartment lined with polyethylene, a hole is cut to drain the juice. Inside put the gauze with apple pulp, shifted boards. A piston cover is placed on top, and a press of one of two structures rests on it:
- worm gear;
- jack.
Screw twist smoothly, watching the drain of juice. At the end of the process, the screw is screwed up, the cake is removed from the gauze.
Apples for the described manual juicer can also be crushed with a mixer mounted on a drill, this will speed up the process. And as a tank, you can use a large plastic bottle.
Useful tips
Watching the video on how to make a juicer, do not forget about the preparation of raw materials for pressing. Apples wash and cut away rotten places. Product for juicers from washing machines to cut and clean is not required, but should remove bones. The resulting dry cake is added to animal feed in the winter and used as a fertilizer.
Having mastered the independent production of the juicer, you can easily to repair factory model.