How to choose a compressor for sandblasting
With the growth of the level of technical solutions, even in a small workshop, you can organize a workplace for sandblasting a variety of materials. This became possible due to the availability of affordable compressors on the market, as well as the availability of a variety of components and consumables, such as nozzles, oil and moisture traps, and abrasive powders.
However, to achieve high productivity and productivity, you need to properly select the equipment. A compressor for a sandblaster must have certain characteristics depending on the surface to be treated. There are also a number of recommendations for building strapping and other parts of the overall technical solution of the toolkit.
Content
Selection of the main characteristics of the compressor
In a variety of reference materials, it is possible to find data that the minimum threshold for compressor performance should be 500 liters per minute at a pressure of 5 bar. However, practically nowhere speaks the truth. You can even choose a compressor for sandblasting with such characteristics. without the necessary strapping. However, with this:
- sandblaster can work only with limited types of surfaces and coatings;
- long-term use of a sandblaster is not ensured - pauses are needed for engine cooling;
- sandblasting compressor will show all its structural features, in particular, rotary models will inevitably give air in spurts.
Based on practical experience of use and recommendations of leading manufacturers of professional equipment, you can derive an honest assessment of the minimum requirements for the injection system. The compressor must necessarily work with strapping in the form of a receiver. With the right choice of its volume, it is possible to achieve the required continuity of work, even if a piston-type supercharger is used.
The main requirements for selecting a compressor for a sandblaster depend on the materials and nature of the coatings with which you will have to work:
- for processing of concrete, chamber surfaces, wall brickwork the minimum level of working pressure should be 3 bars;
- when working with metal, the compressor must provide a pressure of 6 bar;
- to remove durable coatings, the recommended pressure is 9 bar.
The maximum, which should be guided, if you want to choose a compressor for sandblasting with high flexibility - pressure 12 bar. In the recommendations under consideration, it is assumed that the diameter of the working nozzle is 5 mm, and the flow rate indicator is 800 liters per minute.
Choosing the right hose
A major role in the formation of the final parameters of the air-abrasive jet sandblasting is played by the equipment of the apparatus. These are hoses, various connecting elements, sgony, adapters. In order for the compressor power to be used optimally, it is recommended:
- not to allow a change in the diameters of the air passage channel along the route;
- minimize the number of transition elements;
- use durable, non-bendable hoses with a diameter that is 3-4 times larger than the working diameter of the nozzle.
The length of the hose from the air station to the sandblaster should be minimal. A mobile industrial compressor will necessarily take this feature into account. If we are talking about semi-manual installationIt is recommended to increase the length of the hoses by building up the hose going from the compressor to the abrasive-air mixing unit.
You can further increase productivity, reduce downtime and get the right, stable pressure for sandblasting by choosing the type of supercharger.
Select compressor type
The main requirement for the supply of compressed air into the mixing chamber of a sandblaster - uniformity. Therefore, some types of compressors unequivocally benefit from the comparison due to the design features. Others are more common and more affordable. What exactly to choose depends on the planned scope and nature of the work performed.
Piston
Reciprocating compressors are ideal for users who need to produce a small or medium amount of work.. They fit well in the garage, quite unpretentious in winter. However, this type of device has some features.
- Due to the discrete operation of the piston group, the air flows in jerks.
- The device, which is suitable for sandblasting, will be oil type. In such devices, it is possible that the drops of oil in the output air flow.
- The compressor must operate with mandatory stops for cooling.
Important! Piston model without strapping is not suitable for sandblasting machine. Air jerks can cause undesirable surface damage. The flow of oil can cause clumping of the abrasive materialblockage or failure of the mixing unit, unacceptable quality surface treatment.
However, it is better to buy a piston compressor as part of a finished air station. In this case, the device will be equipped with the necessary strapping, which includes:
- a receiver in the role of damping jerks of the drive, removing supply throws and allowing the engine to stop for cooling;
- trap oil installed at the outlet of the compressor;
- gearbox, stabilizing the output pressure;
- trap condensate (moisture), installed at the outlet of the station or part of the pressure reducer.
A properly equipped station is perfect for small workshops. With the right choice of parameters, it will provide the necessary pressure for sandblasting and pumping volume, while not overheating to a stop for a long time.
Screw compressors
The main feature of the screw compressor, valuable for sandblasting machines, is complete no air outlet. Devices of this class:
- practically do not vibrate when working;
- are precisely regulated at the factory and do not require intervention, complex periodic maintenance;
- characterized by very stable performance.
However, screw compressors are not frequent inhabitants of small workshops. The reason is simple: road devices, often focused on fixed installation. Screw compressor generates significant pressure and is characterized by huge air productivity. This type of equipment is rational to use paired with receiver (or several) to supply multiple sandblasting plants.
Electric
Electric compressors are the most common class of equipment. Among the models on the market, you can choose the product of the desired power and performance. However, if we talk about the large-scale use of such devices, it becomes clear that with certain boundary requirements for the volumes and parameters of the supplied compressed air, the use of such compressors economically inefficient. Therefore, places where an electric air compressor is used are limited to small, medium-sized workshops and private garages.
Important! Equipment of this class has another drawback: it requires a powerful source of energy to work.Therefore, an electric compressor is used, so to speak, within civilization, where there are centralized power supply networks.
Diesel and petrol
Diesel and petrol compressors offer tremendous advantages in many ways. For example:
- work without power supply;
- can act in cold weather (diesel ones - provided they are equipped with a special starting system, the so-called winter package);
- in some cases - more economical than electric.
But most importantly, the value of a diesel or gasoline compressor - their energy charge is much higher than electrical devices. With the same mass indicators, the equipment on the internal combustion engine will be much more powerful and productive.. Therefore, often large workshops or production workshops use diesel or petrol compressors.
Important! As another important feature of the equipment with an internal combustion engine can be noted the best cooling mechanics and the possibility of continuous operation over several shifts or around the clock. Therefore, diesel and gasoline compressors are quite popular, offered in a huge range of models, screw and piston type.
Should I buy a used compressor
The secondary market of equipment is very attractive with low prices, it blooms with the assurances of sellers in the style of “included once for testing”, pleases with a variety of compressors for sandblasting. However, considering the used equipment, it is worth not giving in to the external impression. Many products of the secondary market are cosmetics, pre-training. They look great, but this does not affect the nature of the work. If the difficult financial situation makes pay attention to used compressors, it is worth remembering some facts.
- Over time, parametric compressor inevitably falls. Therefore, if you need to buy equipment with high performance, it is better to check it carefully using flow meters and other measuring devices.
- Diesel compressors have the most wear.. The piston group of the engine is destroyed due to the constantly high pressure in the chambers. The engine consumes more fuel at a lower power output, is experiencing difficulties starting with a drop in air temperature. Used equipment of this type will require high maintenance costs, constant cleaning, repairs.
- Screw compressor in the secondary market - real dark horse. Equipment may not comply with the stated specifications. In addition, worn bearings or rotary units will require expensive repair or replacement, with the assistance of specialists or company service. Even worse, if the shutdown of the compressor causes the shutdown of work and the failure of the timing of orders.
- Equipment with non-common types of nodes, lubricants - not the best choice. Especially it concerns products of the Chinese industry and to nobody known brands. In case of failure to repair such a compressor it can be very difficult or impossible due to the inaccessibility of spare parts.
Manufacturers of compressors for sandblasting (when it comes to serious companies) always declare the duration of normal operation for their equipment. Usually this term is 7-10 years old. For this parameter (based on the date of sale or release), you can choose a compressor in the secondary market.
What is the best way to operate the compressor
When working with a sandblaster it is necessary not only to achieve high productivity and the required surface finish. The operator always gets the following task list.
- Achieve as many recovery cycles for abrasive material as possible.
- Avoid undesirable effects on the treated substrate.
- Work in any weather.
- Reduce dust entry in the input path.
To solve the above tasks will allow industrially produced nodes, some of which must necessarily be included in the strapping of the air station.
Neutralization of condensate
Condensate always arises. at the pressure conversion boundary. When the air intake and its compression in the supercharger necessarily condensate, which enters the output path.Receipt of air droplets:
- causes clumping of abrasive sand, which reduces the quality of processing, can disrupt the operation of the mixing unit;
- causes corrosion of some abrasive materials, in particular, steel shot, which reduces the number of recovery cycles and economic efficiency.
It is possible to neutralize the condensate using a compressed gas cooler, after which a cyclone separator / moisture trap is installed.. This set of equipment is installed at the outlet of the supercharger (recommended) or receiver.
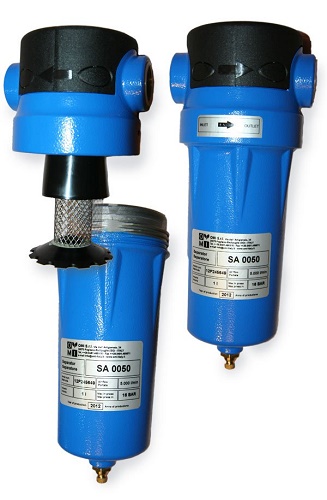
Cyclone separator-moisture trap
Oil neutralization
The presence of oil in the exhaust air stream is a common feature. piston devices. The mechanics of the action of such impurities on the abrasive mixture is similar to the effects of condensate. Except that the oil does not cause corrosion. However, it may be highly undesirable when processing the surface.
Getting on the base, the oil is capable of causing a variety of unpleasant consequences: from disruption of chemical composition, reduction in adhesion, to destruction or discoloration. To neutralize such an impurity in the output air flow is needed special trap. This node should be installed directly at the outlet of the compressor.
Work in the winter
Temperature drop below 0% dangerous for electrical devices. Further reductions in performance can cause problems starting internal combustion engines. It is especially difficult to get a diesel in the cold. Therefore, if you plan to work in the winter in the open air, you should definitely take measures to ensure the proper operating conditions of the compressor.
Electrical devices are to heated body. Such a system can be made independently using thermal sensors and a special heating cable.
Reducing the amount of dust in the input path
The easiest way to eliminate the danger of dust entering the compressor. To do this, apply the scheme.
- To the compressor station, where supercharger and receiver combined in a single design, attach the underwater hose, the end of which is displayed far beyond the working area.
- In systems where compressor and receiver are separatedIt is allowed to extend the route going from the supercharger. The latter is placed away from the work area. It is not recommended to extend the hose from the receiver to the sandblaster.
In some cases, to clean the intake air from dust automotive or special industrial filter. Such equipment will require periodic cleaning of the site or replacement of the work item. However, in cases where it is not possible to clean the input air in another way, it is quite rational to go to such expenses.
Conclusion
Properly selected compressor is a guarantee of high-quality surface treatment with good labor productivity. However, without proper strapping, means of air purification from moisture, oil, to achieve the required continuity and convenience just will not work. Therefore, the choice of equipment should be approached with full attention, not trying to save on key elements or by purchasing used units.