What is the difference between a drill and a hammer drill
Not every master understands the difference between a drill and a perforator, no less questions arise when choosing and buying a tool. At first glance, the difference exists solely in size and cost, but in fact - these are two different power tools. The drill and punch has its own characteristics, its own effective area of use and a large difference in design.
Content
Design features
Despite the similarity of the destination, the hammer drill differs from the perforator not only in many technical parameters, but also in the principle of operation of the percussion mechanism.Design features dictate the optimal area of use of the tool, and this must be understood, otherwise the equipment fails, and the result of the work is unsatisfactory.
Working principle of impact drill
The impact mechanism of the drill is quite simple, without any complicated details. It is based on a mechanical effect. rubbing gears with molded teeth of conical shape, with the help of which the torque is converted into translational. Simply put, the blow is formed from the slippage of gears.
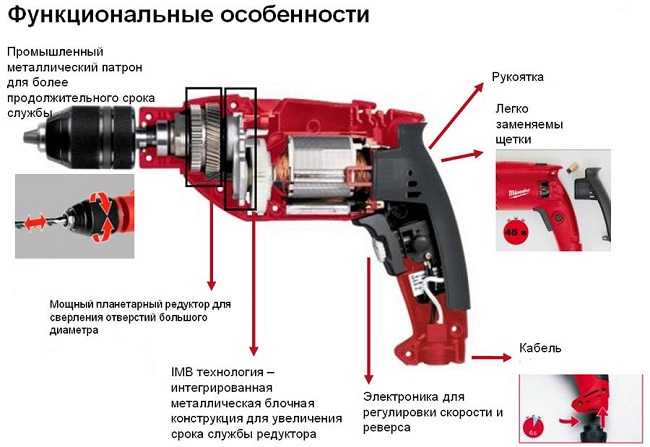
Hammer drill device
The disadvantages of this design are in a small amplitude of oscillation, which is why the force of impact, in comparison with the perforator, is several times weaker. Moreover, this design leads to quick wear gearsexperiencing severe friction under load.
Drilling, as the main task of any drill, does not have a serious load on the mechanism. The only point is that the overload of the motor of a low-powered drill is not excluded, the user must comply with the technical requirements when working.
In the passport to the tool, the maximum dimensions of the holes are always indicated, exceeding the allowable values will have a negative impact on the internal parts.
The principle of the punch
In the perforator, the impact function is implemented using a mechanism of two types, the main of which is pneumaticIt is this type of drive that is able to transmit the maximum possible impact force to the working tooling. The second type is mechanicalIt is a bit similar to the principle of the impact drill, but now it is found in perforators less and less often due to lower efficiency and increased wear of parts.
It is very simple to understand which type of mechanism a punch is - a pneumatic tool with no load does not produce shock movements, unlike a mechanical one, where during operation a blow is made regardless of the working position. This can be determined even visually, when working at idle.
Pneumatic strike is widespread among professional, semi-professional and good household tools. This type of mechanism increases the cost of the punch, but from a practical point of view it is more profitable. Worn gears during mechanical shock will inevitably lead to repair, or rather, replacement of parts, when the teeth are erased, the blow gradually weakens and disappears.
In this way, work on concrete or brick - This is the main function for any punch. The difference is that the models with a pneumatic actuator will be the best option, and the tools with a mechanical shock have a smaller resource and are intended for rare household work.
Modifications of perforators
Perforators can be divided into two large groups according to the type of engine location:
- horizontal;
- vertical.
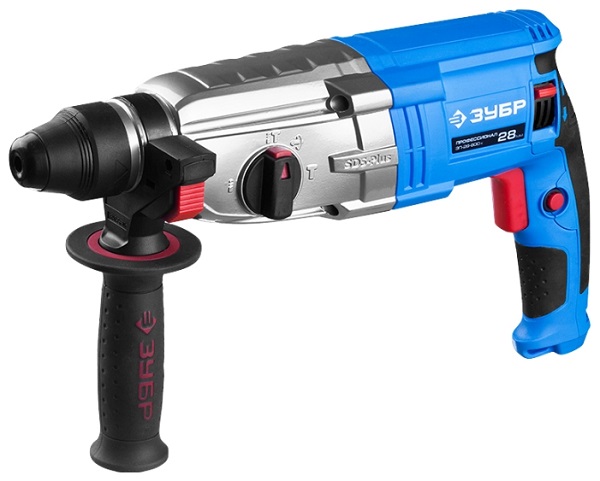
Horizontal Punch
Models with horizontal engine have less weight and are inferior to the "vertical" in all basic characteristics: power, impact force. Horizontal modifications almost always contain the reverse function, and the key is rarely located in the usual place on the button. There are models where the reverse is displayed by a separate key or a slider on a brush collector assembly, in which air vents sparks can appear. Vertical engine layout increases tool productivity, which makes it possible to drill deep holes of large diameter.
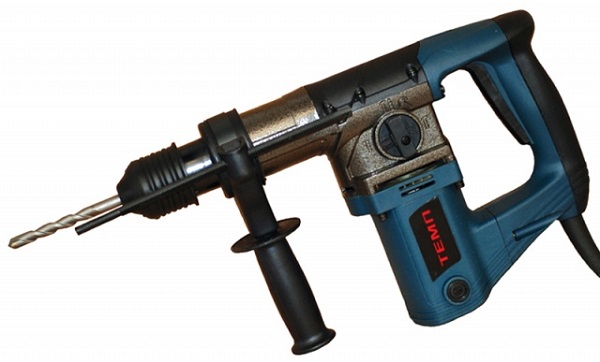
Vertical Puncher
There is one more modification of perforators - it is industrial models with chuck SDS-MAX. Despite the name "perforator", in fact it is a lightweight and compact version of a jackhammer. Such tools can be used for normal work, using the SDS + / SDS-MAX adapter, ordinary drills are installed, but they are too heavy and powerful.
Power factor for drills and drills
The power of impact drills mainly varies in the range from 500 to 1050 watts. The most common versions with characteristics from 600 to 800 W, this is due to their low cost. But it is more powerful than models to reasonably prefer an inexpensive punch: with a similar cost, the efficiency of the drill’s impact force will be much lower.
The power range of horizontal perforators is from 700 to 1000 W and vertical ones up to 1500 W. The average value of the force of blows is 3 J, while for the top industrial-class models it is even higher.
There is an erroneous opinion that the power directly determines the performance of the punch. It is not uncommon when a model with a good power rating when drilling is weaker than a less powerful counterpart. In addition to the number of watts, on the quality of work affects impact strength indicatormeasured in joules (j). No less important is such a characteristic as the number of blows per minute; it is this rate that determines the drilling rate.All these indicators are always indicated in the instructions, and they should be paid attention to.
When two tools are presented to the buyer with the same values of watts and joules, performance will be determined precisely by the frequency of beats per minute.
At the drill, on the contrary, power is a factor determining productivity. In addition, the higher the rate, the larger the diameter it can drill, the longer it can work without interruption.
The main purpose of the tools
Each tool has its own optimal area of use. A hammer drill or perforator is designed for certain types of work, but they are similar in their functionality, and sometimes they are capable of replacing each other.
Design features directly determine the available range of work for a particular model. Accordingly, the purchase of an instrument should be based not only on technical parameters, but also on the user's needs.
Impact Drill Functionality
Impact electric drills perform several functions:
- drilling wood, metal, plastic, rubber, glass, ceramics;
- tightening screws (in the presence of reverse);
- drilling concrete and bricks.
Despite the fact that almost all the models currently being produced have the function of drilling with a punch in their arsenal, this does not at all mean that they can replace a punch. This is due to the fact that the main task of the drill is in the usual drilling, because its design is not designed for long-term impact loads when drilling concrete. In short, the impact function of a drill is just an additional option, intended for one-time short-term use.
Reverse allows you to tighten and unscrew the screws, but the lack of installation of torque, like a screwdriver, makes the function secondary. With experience and skill, the drill can only partially replace the power screwdriver.
The main purpose of the punch
In contrast to the hammer drill, the main task of the punch is impact drilling and chiselling (work on concrete, brick). To realize these functions, the perforator has a more reliable design, which allows the tool to easily carry long impact loads. Due to the implementation of a much greater force of impact, all the work performed is carried out easier and faster.
Naturally, in horizontal and vertical perforators, the application area varies slightly. This is due to different technical characteristics, therefore, the capabilities of the tools are also different.
Horizontal versions perforators according to their technical data are convenient for use at home or in the country. Under professional conditions, they are acquired for intensive drilling of holes up to 16 mm in diameter and less than 30 cm in length. Light weight will allow to operate the tool for a long time on weight, for example, when installing doors or stretch ceilings.
Perforators with a vertical engine used for laying pipes or chroming. Tools of this class are much more expensive and are purchased exclusively for highly specialized works. Industrial models SDS-MAX are used for chiselling concrete, for example, when it is necessary to make a door or window opening in the wall.
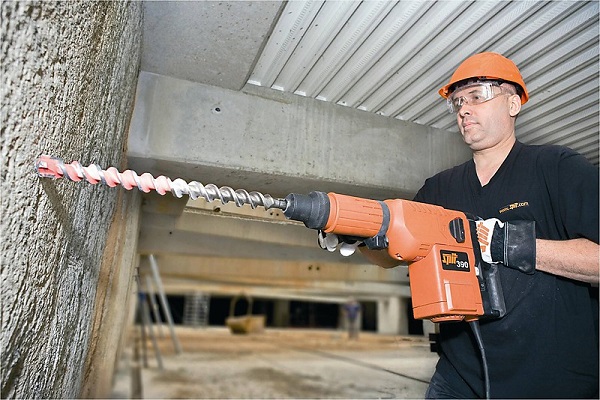
Puncher Spit 390 SDS Max
Types of attachment accessories drill
The drill chuck of the impact drill allows you to install standard drill bits with a straight shank. They are used for drilling various materials, such as wood or glass. The cartridges themselves are of two types - keyless, they are also called quick-clamping, and cartridges, where the fastening of the drill occurs by tightening with a special key.
The advantage of this type of cartridges is that they can clamp drills of small diameters, up to 0.8 mm. At the same time, the equipment is fixed exactly, without distortions, and there are practically no fluctuations during operation. The disadvantage of this design lies in the relatively limited diameter of the snap up to 13 mm.
On sale there are "consumables" of a larger diameter with a fit of 13 mm, but they are more expensive and less common than standard ones. There are larger chucks, but they are mainly installed on low-speed drills, which lack the function of impact.
Cases are not excluded when, at load, the drill begins to stop, while the cartridge continues to rotate. The reason lies in the fact that there are no “hooks” in the cam cartridge, and the cylindrical shank of the drill is smooth. The drill chuck is designed for ordinary drills only. adapters for borax does not exist.
Type of attachment punch snap-in
Unlike the impact drill, the punch tool is attached to the drill chuck in a different way.For this purpose, the mount provided special latchreliably fixing the drill in the boss. To install the "consumables", you need to attach the drill shank to the chuck and slightly press down when the snap-in snaps into place you can hear a characteristic click. To extract the drill, it is necessary to press on the moving part of the cartridge and remove the tooling, but there are also such cartridges where you need not to press, but turn it to the side.
Type of Mounts is called SDS, and is divided into two categories: SDS-MAX, this mount is most often found on industrial-grade tools, and the more common SDS +, with which almost all light and medium drills are equipped. Also included in the package of light models as a supplement is a drill chuck of the same system as the impact drill. Install it into the cartridge punch through a special adapter.
Drill chuck greatly expands the capabilities of the punch, allowing you to use conventional drill bits with a cylindrical shank. In this case, any model can replace a hammer drill, but is suitable only for rough work.
Choosing an adapter for the cartridge, you need to pay attention to its marking and type of cartridge. The fit and thread pitch of the cartridges is different (20UNF, 24UNF, B16 or others), they are not interchangeable, because the 24UNF adapter is not suitable for the B16 or 20UNF cartridge. For SDS + and SDS-MAX cartridges, different drills are used, with the corresponding shank. They are easy to distinguish visually, landing SDS-MAX is much wider than the SDS +, but there are various adapters for rigging available.
findings
The design and technical characteristics of the impact drill and perforator indicate that these are different tools, and it cannot be said that one is better than the other. Need to use them by appointment, based on the parameters and the specific task, and if drilling for a powerful perforator is easy work, then drilling of concrete with a drill leads to rapid wear.
The most successful, thoughtful and versatile tool - horizontal punch. He is able to replace the impact drill, to perform a number of tasks for drilling various materials. When it is necessary to make a choice in favor of one tool - the choice is obvious.